IMPLANT TARGET PLATE

The goal for this project was to provide a target plate that could withstand an estimated 8KW of thermal energy while housing 2", 4", and 6" silicon wafers inside a high vacuum chamber. The target plate also required the capability to tilt to specified angles during process. Water and gas cooling was routed to this fully enclosed target plate to dissipate the high thermal energy.
The scope of my work for this project consisted of the complete mechanical design of this target plate.
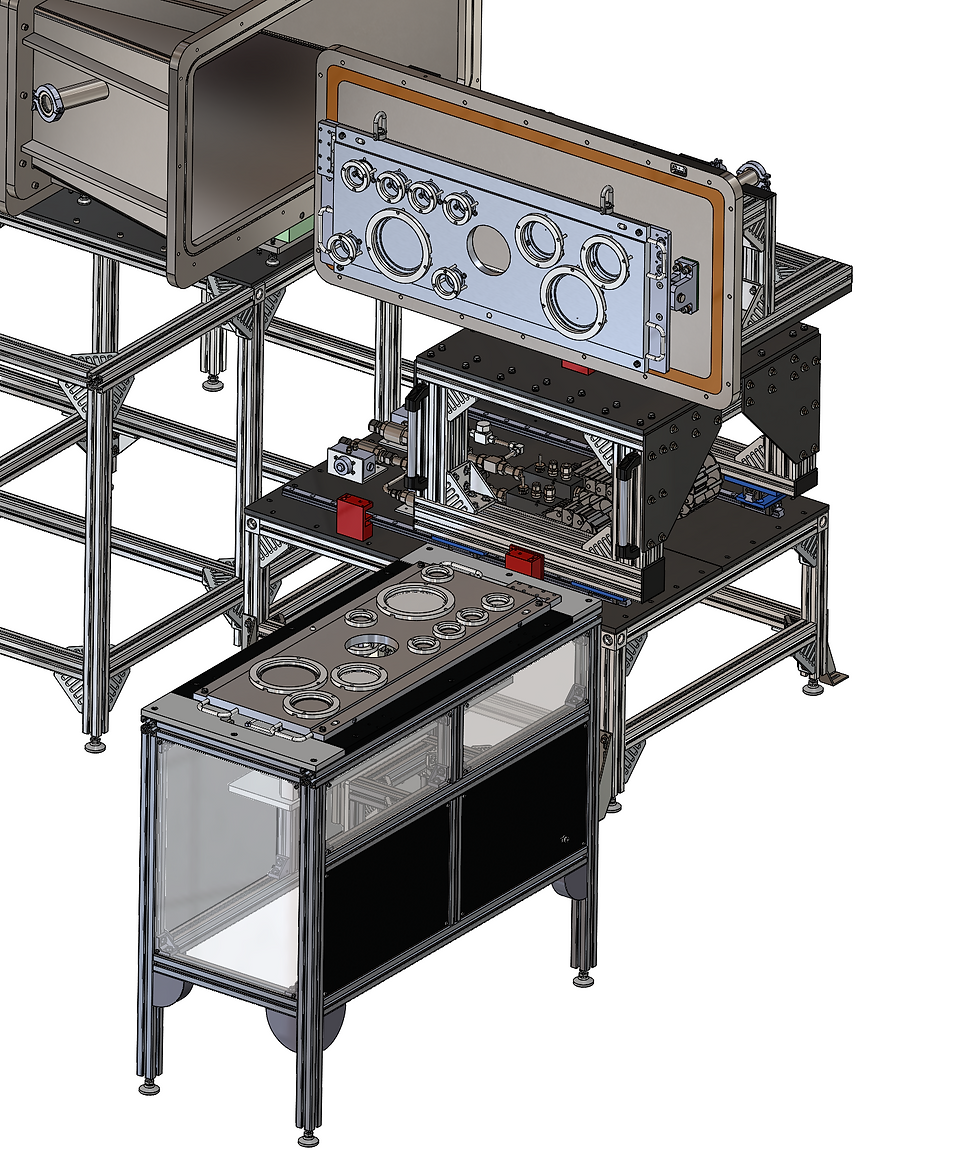
The target plate held a total of six 2" wafers, two 4" wafers, and two 6" wafers

A custom designed clamping mechanism was developed to hold wafers in place during process. The use of springs on the opposite side of the target plate gave the necessary force to clamp the wafers in place while still providing a small enough form factor to fit inside the chamber.
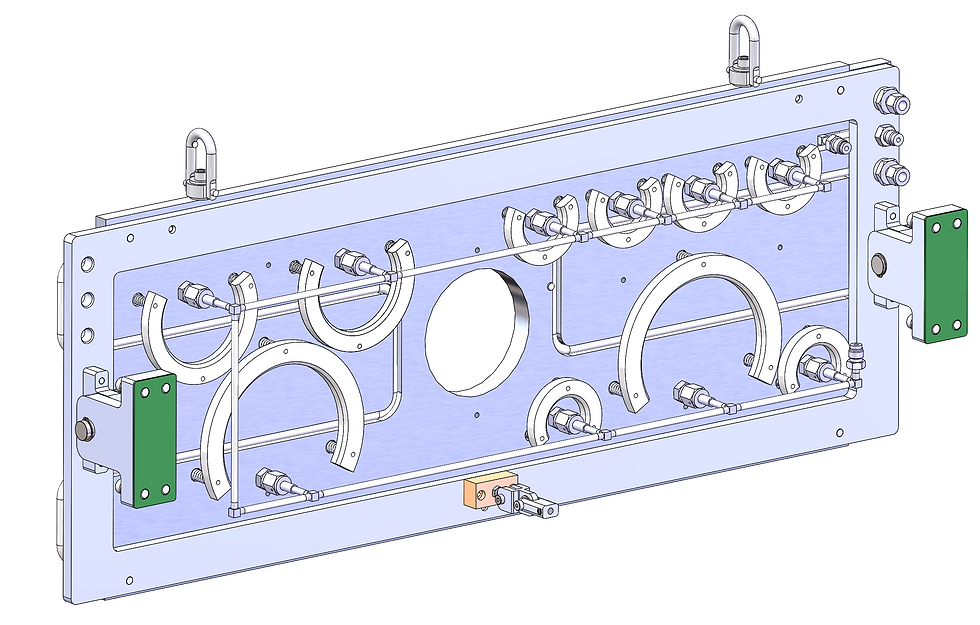
A custom designed gasline was made to provide backside gas cooling. Welded stainless steel tubing, and Swagelok VCR connectors were used to ensure leaks were eliminated inside the chamber.
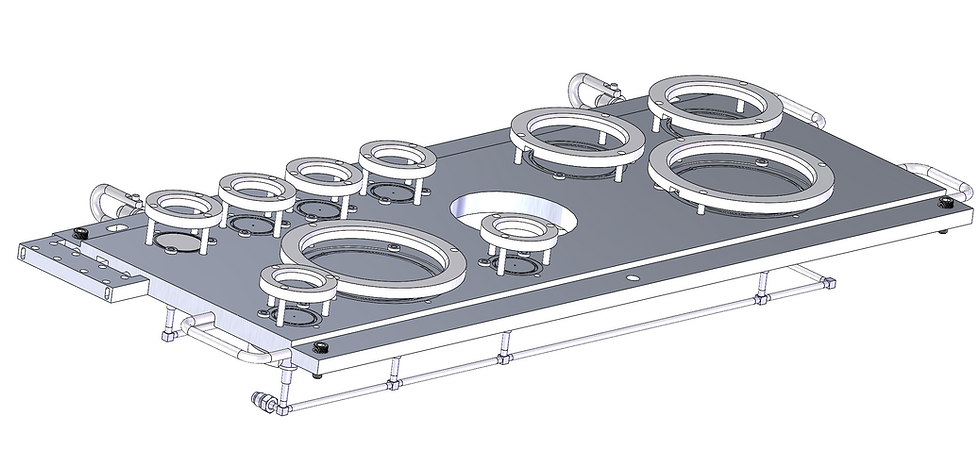
O-ring's were used to maintain seal for backside gas cooling and prevent gas leakage inside the chamber

A stepper motor coupled with a linear ballscrew bellows drive allowed for the necessary tilt positioning while under high vacuum

Simulations were done to verify the efficiency of the water cooling channels, as well as the back side gas cooling

The required supplied inlet water pressure, and volumetric flow needed was verified by simulation.
